Berkeley Lab Researchers Use Fluorescent Tetrapod Quantum Dots to Measure the Mechanical Strength of Polymer Fibers
JULY 29, 2013
(510) 486-5375
Feature
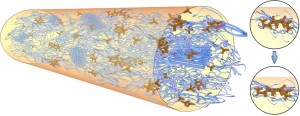
Fluorescent tetrapod quantum dots or tQDs (brown) serve as stress probes that allow precise measurement of polymer fiber tensile strength with minimal impact on mechanical properties. Inserts show relaxed tQDs (upper) and stressed tQDs (lower).
In a study led by Paul Alivisatos, Berkeley Lab director and the Larry and Diane Bock Professor of Nanotechnology at the University of California (UC) Berkeley, the research team incorporated into polymer fibers a population of tetrapod quantum dots (tQDs) consisting of a cadmium-selenide (CdSe) core and four cadmium sulfide (CdS) arms. The tQDs were incorporated into the polymer fibers via electrospinning, among today’s leading techniques for processing polymers, in which a large electric field is applied to droplets of polymer solution to create micro- and nano-sized fibers. This is the first known application of electrospinning to tQDs.
“The electrospinning process allowed us to put an enormous amount of tQDs, up to 20-percent by weight, into the fibers with minimal effects on the polymer’s bulk mechanical properties,” Alivisatos says. “The tQDs are capable of fluorescently monitoring not only simple uniaxial stress, but stress relaxation and behavior under cyclic varying loads. Furthermore, the tQDs are elastic and recoverable, and undergo no permanent change in sensing ability even upon many cycles of loading to failure.”
Alivisatos is the corresponding author of a paper describing this research in the journalNANO Letters titled “Tetrapod Nanocrystals as Fluorescent Stress Probes of Electrospun Nanocomposites.” Coauthors were Shilpa Raja, Andrew Olson, Kari Thorkelsson, Andrew Luong, Lillian Hsueh, Guoqing Chang, Bernd Gludovatz, Liwei Lin, Ting Xu and Robert Ritchie.
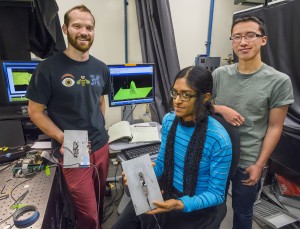
From left, Andrew Olson, Shilpa Raja and Andrew Luong are members of Paul Alivisatos's research group who used electrospinning to incorporate tetrapod quantum dot stress probes into polymer fibers. (Photo by Roy Kaltschmidt)
“Understanding the interface between the polymer and the nanofiller and how stresses are transferred across that barrier are critical in reproducibly synthesizing composites,” Alivisatos says. “All of the established techniques for providing this information have drawbacks, including altering the molecular-level composition and structure of the polymer and potentially weakening mechanical properties such as toughness. It has therefore been of considerable interest to develop optical luminescent stress-sensing nanoparticles and find a way to embed them inside polymer fibers with minimal impact on the mechanical properties that are being sensed.”
The Berkeley Lab researchers met this challenge by combining semiconductor tQDs of CdSe/CdS, which were developed in an earlier study by Alivisatos and his research group, with electrospinning. The CdSe/CdS tQDs are exceptionally well-suited as nanoscale stress sensors because an applied stress will bend the arms of the tetrapods, causing a shift in the color of their fluorescence. The large electric field used in electrospinning results in a uniform dispersal of tQD aggregates throughout the polymer matrix, thereby minimizing the formation of stress concentrations that would act to degrade the mechanical properties of the polymer. Electrospinning also provided a much stronger bond between the polymer fibers and the tQDs than a previous diffusion-based technique for using tQDs as stress probes that was reported two years ago by Alivisatos and his group. Much higher concentrations of tQDs could also be a achieved with electrospinning rather than diffusion.
When stress was applied to the polymer nanocomposites, elastic and plastic regions of deformation were easily observed as a shift in the fluorescence of the tQDs even at low particle concentrations. As particle concentrations were increased, a greater fluorescence shift per unit strain was observed. The tQDs acted as non-perturbing probes that tests proved were not adversely affecting the mechanical properties of the polymer fibers in any significant way.
“We performed mechanical tests using a traditional tensile testing machine with all of our types of polymer fibers,” says Shilpa Raja, a lead author of the Nano Letters paper along with Andrew Olson, both members of Alivisatos’ research group. “While the tQDs undoubtedly change the composition of the fiber – it is no longer pure polylactic acid but instead a composite – we found that the mechanical properties of the composite and crystallinity of the polymer phase show minimal change.”
The research team believes their tQD probes should prove valuable for a variety of biological, imaging and materials engineering applications.
“A big advantage in the development of new polymer nanocomposites would be to use tQDs to monitor stress build-ups prior to material failure to see how the material was failing before it actually broke apart,” says co-lead author Olson. “The tQDs could also help in the development of new smart materials by providing insight into why a composite either never exhibited a desired nanoparticle property or stopped exhibiting it during deformation from normal usage.”
For biological applications, the tQD is responsive to forces on the nanoNewton scale, which is the amount of force exerted by living cells as they move around within the body. A prime example of this is metastasizing cancer cells that move through the surrounding extracellular matrix. Other cells that exert force include the fibroblasts that help repair wounds, and cardiomyocytes, the muscle cells in the heart that beat.
“All of these types of cells are known to exert nanoNewton forces, but it is very difficult to measure them,” Raja says.
“We’ve done preliminary studies in which we have shown that cardiomyocytes on top of a layer of tQDs can be induced to beat and the tQD layer will show fluorescent shifts in places where the cells are beating. This could be extended to a more biologically-relevant environment in order to study the effects of chemicals and drugs on the metastasis of cancer cells.”
Another exciting potential application is the use of tQDs to make smart polymer nanocomposites that can sense when they have cracks or are about to fracture and can strengthen themselves in response.
“With our technique we are combining two fields that are usually separate and have never been combined on the nanoscale, optical sensing and polymer nanocomposite mechanical tunability,” Raja says. “As the tetrapods are incredibly strong, orders of magnitude stronger than typical polymers, ultimately they can make for stronger interfaces that can self-report impending fracture.”
This research was primarily supported by the DOE Office of Science.
# # #
DOE’s Office of Science is the single largest supporter of basic research in the physical sciences in the United States, and is working to address some of the most pressing challenges of our time. For more information, please visit the Office of Science website atscience.energy.gov/.
Additional Information
For more about the research of Paul Alivisatos go here
No comments:
Post a Comment